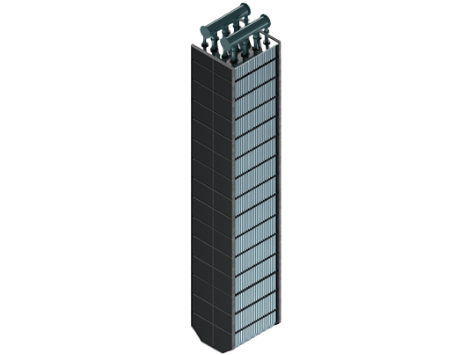
Gas Gas
Heater [Cooler and Re-heater]
It is an equipment for heating out exhaust gas with the purpose of reducing the white plume phenomenon in a flue. Unlike the existing ones, GGH (cooler and reheater) scaled up by KLES has been evolved into a kind of Eco-Efficient product so that the damaged tube alone can be replaced individually, which was originated and engineered by homegrown technology adopting modularized frame system enabling replacement of only a part of suspension supporting the tube bundle.
The Need
Shoring up eco-friendly industrial competitiveness through the localization of clean gas reheating technology for desulfurization: In the desulfurization process of boiler exhaust, flue gas passes through a cooler and then undergoes desulfurization (SO2 removal) in an absorption tower. During this process, as the gas passes through the absorption tower, its temperature decreases, leading to the white smoke phenomenon. To mitigate such plumes, a pressing need arises to develop a localized reheater designed to reheat clean gas making use of the heat absorbed from the cooler.
Cost savings through partially replaceable maintenance Gas-Gas Heater (GGH): The GGH currently in use cannot be maintained partially. Once the tube closure rate exceeds 10%, the entire unit has to be scrapped as a whole, incurring significant operating costs. Hence, there is a need for a GGH available for partially replaceable maintenance solely for damaged tubes.
Original Features
Since the tube itself is manufactured with Teflon, it boasts excellent properties in acid resistance, chemical resistance, and durability; advantageously with a flexible shape, which makes it much easier to maintain and replace the tube itself.
Improved thermal efficiency by the effect of the increased heat transfer areaThe heat transfer area of the developed has been expanded about by 9% compared to the existing one.
Optimized design for improving draft powerWith the optimum design working out tube dimensioning and interspacing, achieving the greater effects in improving differential pressure occurrences, such as in temperature distribution, static pressure distribution, flow rate distribution, draft power, etc.
Durability optimal design, with minimum wear & tear damages to the designed tubeTube damage can be minimized by expanding the tube contact area with the installation of a separate tube fastener.
Improved maintainability, feasible to replace by each tube damagedThe existing product has such a structure where the tube is locked up to the header box that the bundle itself has to be replaced wholly when its blockage ratio exceeds 10% after plugged in because it is unavailable to repair or replace the damaged tube individually.
With the intent to step up maintainability, KLES has researched and introduced modularized GGH designed with a structure so that the Teflon tube can be individually assembled with a self-devised connector. When the tube is damaged or clogged, only the damaged tube can be independently replaced. Moreover, by simply opening a manhole, a worker can enter the duct and afford to replace the damaged tube instantly therein, without wasteful removal of the bundle as a whole.
Upskilled design for better maintainability and convenienceThrough the improvement of the header pipe, the system becomes able to avoid interference with the surrounding environment and importantly, shorten the time required for onsite maintenance.
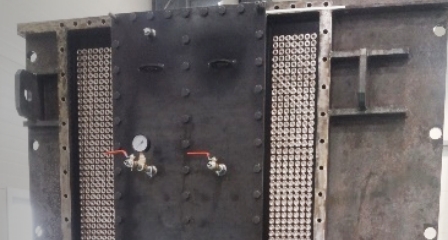
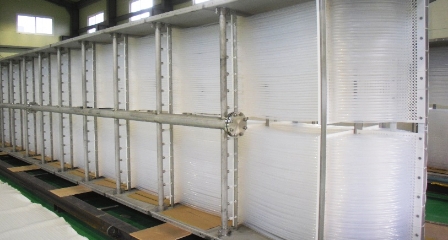
Certificate & Patent
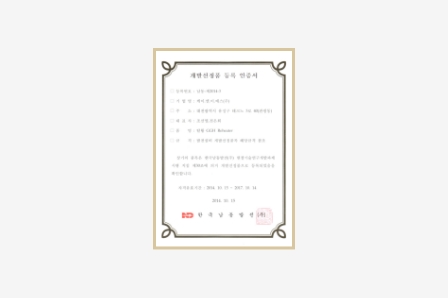
Desulfurization GGH Reheater
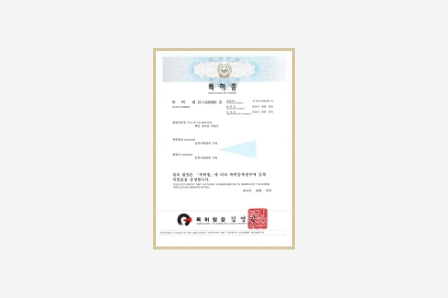
White plume removal heater
Track Records
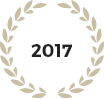
- KOWEPO - Pyeongtaek pp.
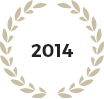
- KOEN - Yeosu pp. #2
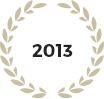
- KOEN - Yeosu pp. #2