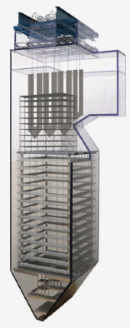
SKYFFOLDINGTM Systems
Platform-supported boiler in-furnace scaffolding & lifting systems
SKYFFOLDING™ Systems, A flagship brand of KLES, first off build up 'Hydraulic lifting system'
on the topmost of the boiler (Heavy girder), and then platform-supported pendant scaffolds
assembled at ground/Zero level are lashed down with wire ropes and lifted up at 2m intervals to
systematize the upper & the lower scaffold system each, whereupon stepping up work
efficiencies by way of stabilization of the system with minimized swaying, while proactively
warding off workplace disaster arising from the chain reaction triggered by a failure of a
member component, as often seen with traditional upright scaffolds.
Currently, the system
has been adopted and operated in most domestic thermal power plants in Korea with over
98%.
Product Configuration
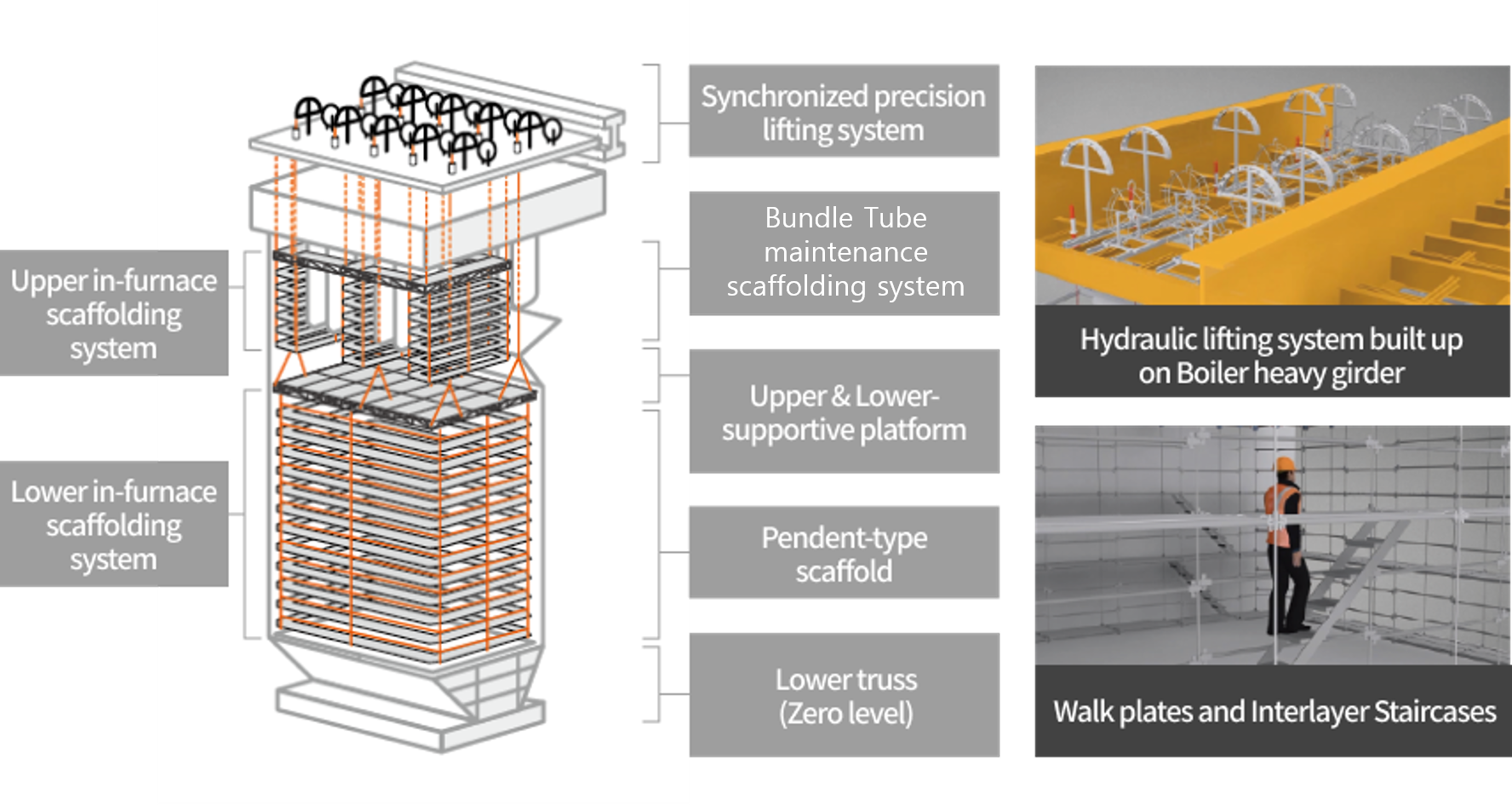
A synchronous system capable of lifting safely with load distribution, keeping up lateral and vertical deviation to a minimum.
Upper scaffolding system to inspect and repair Bundle tubesWorkable for either planned preventive maintenance or contingency maintenance for Bundle tubes on the section of SH Platen and Division.
Lower scaffolding system to inspect and repair Wall tubesAssembled at Zero Level and then lifted up, distributing the loads with minimizing the risk of progressive collapse. Besides, even more precise repair work can be carried out, by installing the walk plates against all 4 sides of the water wall.
Lower truss (Ground/Zero level)Assembling the upper & lower supportive Platform after construction of the foundation structure up to Zero (0) level (Slop tube).
The Need
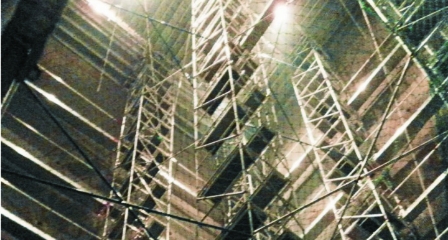
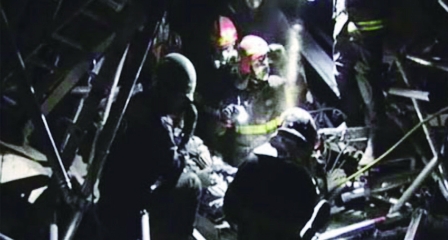
Problems raised to existing tower-type scaffolding: The existing tower-type in-furnace scaffolding system, used to maintain and repair the boilers in thermal power plants, resorts to the erection method of stacking scaffolds from the bottom up. When putting up and taking down the scaffolds, the work has to take place inevitably at high places in danger. Furthermore, since all the loads of the system get concentrated to the bottom, it may well lead to the collapse of the whole scaffold system if triggered by missing or breakage of even a tiny part of members. Such workplace accidents brought on by scaffold collapse would be liable to end up with fatal life injuries and losses, while collateral boiler damages and prolonged repair periods give rise to cutting back power production, on the other hand, thereupon incurring considerable financial losses.
A paradigm shift in Scaffold Industry, Cloud Ladder SKYFFOLDING™ Systems!: This innovative top-down scaffold systemizer and its exclusive construction method not only ward off the onset of chain collapse of in-furnace scaffolding but also minimize high-site operations by means of enabling working on ground zero level for assembly and disassembly, thus avoiding safety accidents. In addition, by putting staircases in between scaffold layers instead of ladders, mobility and workability have been greatly improved.
Safety-shield Features
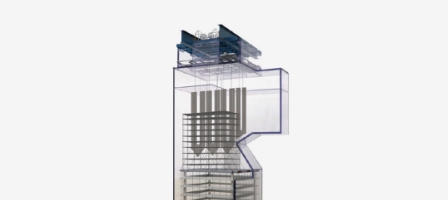
On the heavy girder in the penthouse of the boiler, the strand lift jacks are installed, and then thereto connected by the strand down to the platform which supports the upper and lower parts of the system, so that all the loads can be supported from the top.
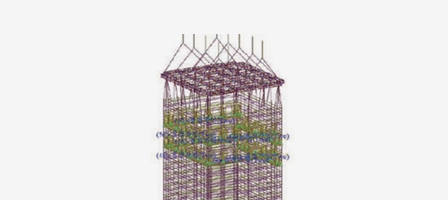
Structural safety and stability have been secured by verifying the stress and strain amounts at the upper support points when the loads are applied to downward scaffolds. In addition, the working loads on the scaffold have been figured out and reviewed to the extent to work by 20 persons in one layer of all 4 sides, or by 5~6 persons on each side.
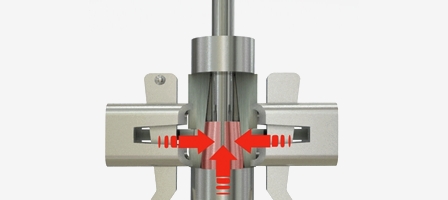
The more load is applied, the farther the clamp tightens the wire rope, therewith beefing up its clamping force.
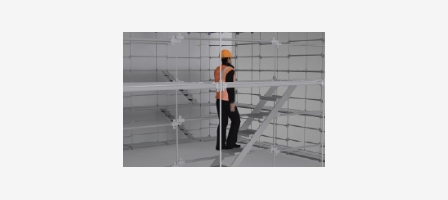
Walk plates designed to ensure easiness and convenience for working, together with staircases
put in between layers taking mobility into consideration.
In an effort to reduce manufacturing costs and improve
installation conveniences, the prefabricated system scaffold components and members are
put into use.
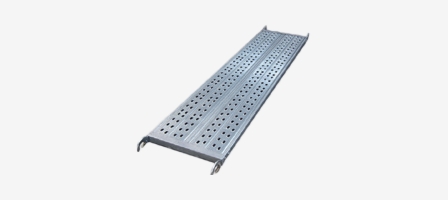
Perfectly improving work efficiencies in detail inspection and repairs by way of putting up walk plates on all fronts against four sides of the water wall.
SKYFFOLDINGTM installation video
Erection Procedures
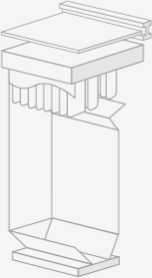
Locating and Selecting Roof wall tube holes suitable for avoiding interferences with Boiler internal tubes and HDR on top of the boiler.
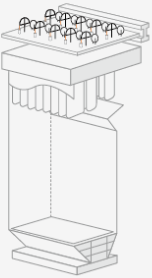
- Building up lifting devices and load-fixture devices at selected locations
- Putting up overall walk plates with Truss structures up to the Zero level.

Assembling and systemizing the wire-rope type scaffolds while lifting the assembled upper scaffolding platform.
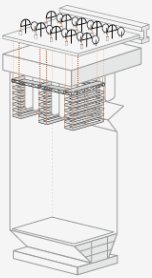
Bespoke designing to be perfectly optimized for Bundle tube maintenance.
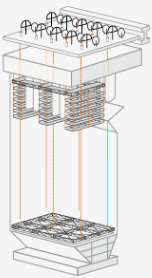
Tying up the assembled Lower scaffolding platform onto the Strand of the lifting system
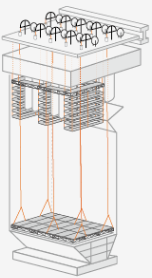
Assembling and systemizing the wire-rope type scaffolds while lifting up the Lower scaffolding platform mounted with uppermost overall walk plates.
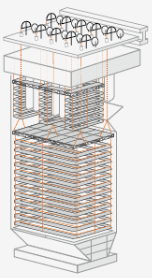
Last off, Completing the construction of the SKYFFOLDING™ Systems by putting up walk plates onto all 4 sides of the water wall, by way of lifting up the platform by 2 meters each for one layer of scaffolding.
SKYFFOLDINGTM installation video by power plant boiler capacity
Comparative Advantages
Item | Tower-type Scaffold | SKYFFOLDING™ |
---|---|---|
Workplace accident avoiding technology |
|
|
Easy to Work with |
|
|
Work efficiency |
|
|
Customized fabrication and service available according to the specific customer needs
Certificate and patent
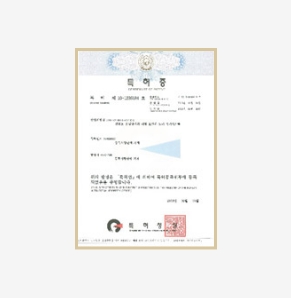
Pendent assembly type scaffolding system for large scale boiler furnace
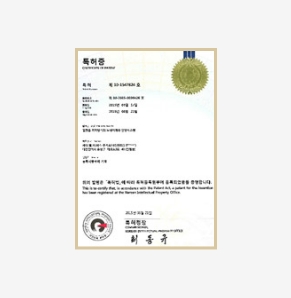
Platform-supported in-furnace scaffolding and lifting systems
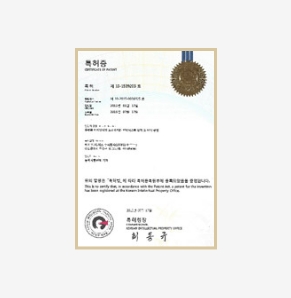
Installation & disassembly methodology for platform-supported in-furnace scaffolding and lifting systems
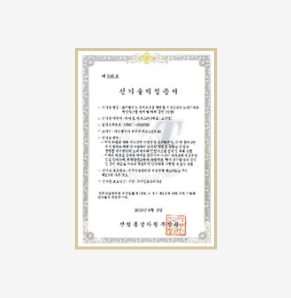
Installation and disassembly methodology for in-furnace scaffolding and lifting systems
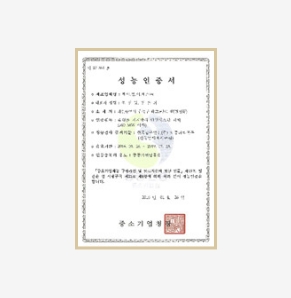
Platform-supported lifting system scaffolds
Track records
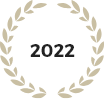
- KOEN - Youngheung pp. #1~4
- KOMIPO - Shin-Seocheon pp. #1
- GEP - GEP pp. #1, 2
- KOSPO - Hadong pp. #7, 8
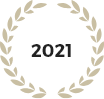
- GGP - Gosung-hi pp. #1, 2
- KOWEPO - Taean pp. #7, 8
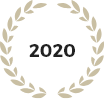
- KOEN - Samcheonpo pp. #5, 6
- KOMIPO - Jeju pp. #2, 3
- EWP - Dangjin pp. #1~4
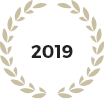
- Hyundai Greenpower - Dangjin pp. #1~8
- GSDEP - BukPyong pp. #1, 2
- HGP - Dangjin pp. #1, 2
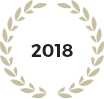
- KOMIPO - Boryeong pp. #3, 6~8
- KOMIPO - Shin-Boryeong pp. #1, 2
- EWP-Dangjin pp. #9, 10
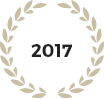
- KOEN - Yeongheung pp. #5, 6
- KOSPO - Samcheok pp. #7~10
- KOSPO - Hadong pp. #1~6
- EWP - Dangjin pp. #5~8
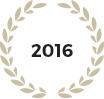
- KOEN - Samcheonpo pp. #1, 4
- KOWEPO - Taean pp. #5, 6
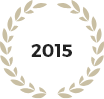
- KOSPO - Hadong pp. #7, 8
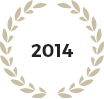
- KOEN - Samcheonpo pp. #1, 2