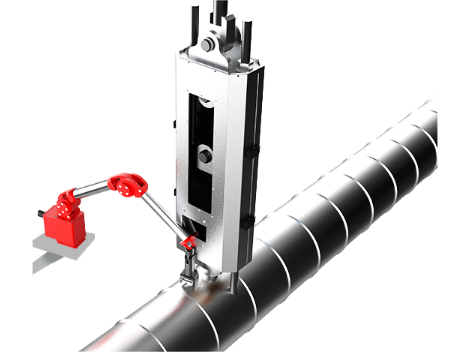
SPPMS Smart Power Piping Management System
SPPMS is a piping management solution geared to power plants, beefed up with real-time pipe status monitoring and life assessment technology. Power generation pipes exposed to high-temperature and high-pressure environments are to deteriorate and deform with ease, which causes damage to the piping system. Such damage to the piping can trigger the failure of the main unit or peripherals, even worse, likely leading to the shutdown of the power plant to incur huge socio-economic losses.
SPPMS monitors the condition of pipes in real time, which comprises a '3D pipe displacement measuring device' measuring realtime 3D movements of power piping, a 'Temperature monitoring sensor' sensing the temperature, and an 'Applied load measuring device' measuring the self-weight and the load; and puts forth a holistic set of data on the condition of the piping system, which can be comprehensively assessed and interpreted to predict and prevent potential pipe accidents proactively.
The Need
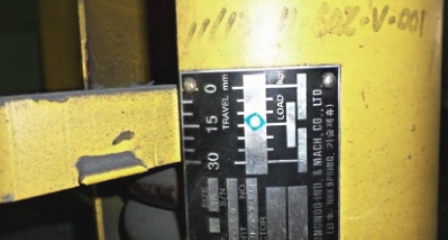
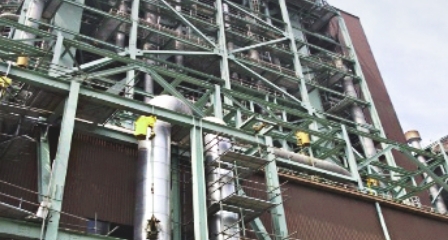
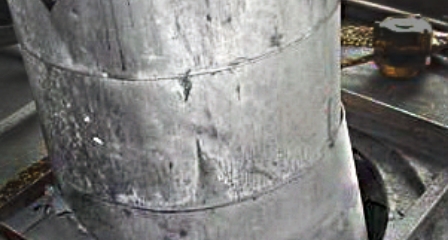
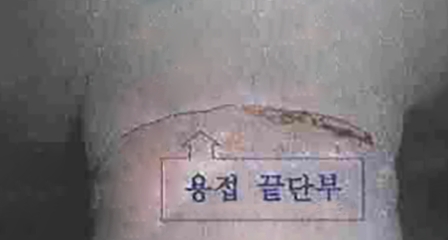
The need for systematic pipe management has arisen: Pipes for power generation are liable to material degradation, and mechanical degradation and deformation due to harsh operating conditions in which they are used for long periods of time under high temperatures/pressures. In addition, thermal expansions & contractions, resulting from frequent vibrations and repetitive mobilizations & shutdowns, cause interference in or restraint on, and stress concentration on pipes; furthermore, may lead to turbine vibration and damage to super-heater connections.
Unavailability to trace 3D displacement: Even today, the piping management system by individual power plants remains limited to retaining records solely of hanger indicator travels before and after overhaul, leaving 3D displacement movement that occurs in pipes during operation entirely unmeasurable and untraceable. Likewise, the plant has been dependent only on short-term maintenance practices so far, making it unaffordable to map out fundamental proactive measures.
Economic losses sustained due to pipe damage: Since pipes are installed geometrically in a 3D structure, they are liable to go through unexpected damages like cracks and ruptures, in the case that they fail to expand to the extent of the design, or they expand over the extent, due to malfunctioning of pipe supporting devices, interferences with the structure, errors in pipe design, or similar issues. Such damages happen to give rise to sudden plant knock-off and the subsequent need for repairs, incurring huge socio-economic losses therewith.
The Necessity of monitoring the displacement and working load of pipe supporting devices: In every power plant, a large number of pipe supporting devices like hangers and snubbers are put in for the purpose of supporting the self-weight and thermal expansion load of the pipes. However, it may happen more often to overlook the crucial timing of essential maintenance for these supporting devices because it is not intuitively easy to sort out the cycles for the maintenance and reparation for such devices.
Obstruction to the inspection of pipe supporting devices at heights and Exposure to safety accidents thereon: Since most pipe supporting devices are located in hazardous areas at heights or of high temperatures, the accessibility is too virtually obstructed to carry out detail inspection, along with exposure to safety accidents.
Venue Photo
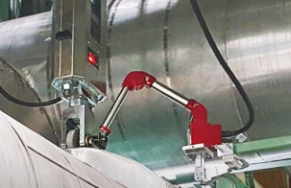
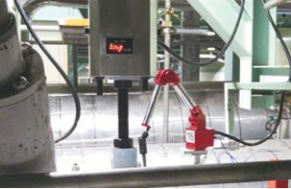
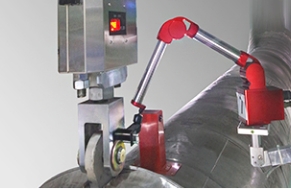
Smart Intelligence System
Featuring real-time remote monitoring against changes in 3D movements such as pipe displacement, temperature variations, and load irregularities.
Pipe Integrity and Safety securedBy way of a comparative analysis between the original design value set (design displacement) and the displacement resulting from the operation (operation displacement), the pipe accident can be predicted, whereupon the measures required for such piping can be taken swiftly so that the integrity and safety of piping can be maintained in one piece.
Working At Height [WAH] avoidedMost pipe support devices are situated in hazardous areas such as high places and high temperatures/pressures, which makes it not easy to access them. Introducing SPPMS workable to monitor the piping remotely can prevent safety accidents preemptively.
Usable as the basic data to analyze causes of pipe stress and damagesData Data purposed to diagnose the condition of pipes are being collected in real time in SPPMS, which can be compatibly utilized as a basis for prognosing and sorting out overall pipe damage problems.
Product Diagram
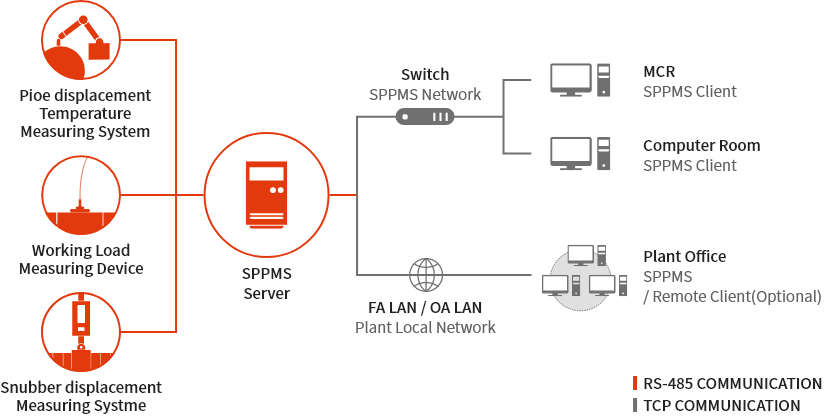
SPPMS Management Programs
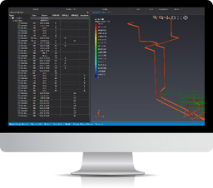
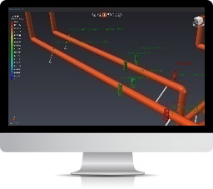
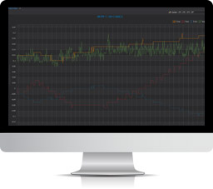
Field | Description |
---|---|
Pipe information management | Pipe-related information management and querying |
Realtime pipe monitoring | Realtime data retrieval and alarming |
Realtime data and trends querying | |
Realtime hanger load monitoring | Realtime data retrieval and alarming |
Realtime data and trends querying | |
Realtime snubber displacement monitoring | Realtime data retrieval and alarming |
Realtime data and trends querying | |
Pipe life assessment management | Pipe stress component querying |
Realtime fatigue life and creep life querying |
Furnishing customized services, with the products and solutions to suit specific client requirements
Certificate & Patent
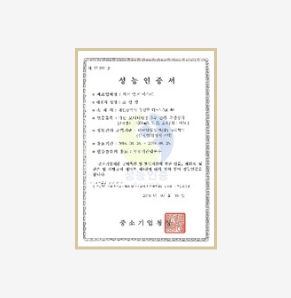
Pipe monitoring, Tri-axial Displacement measuring device
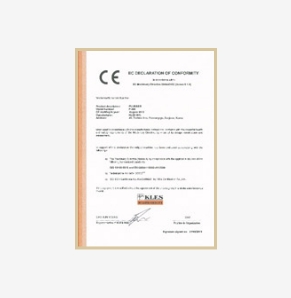
PLUMBER _3D Displacement measuring device
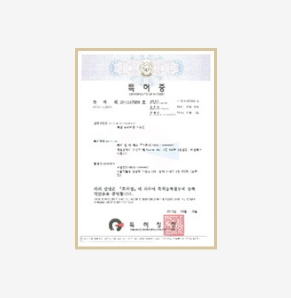
Pipe monitoring system
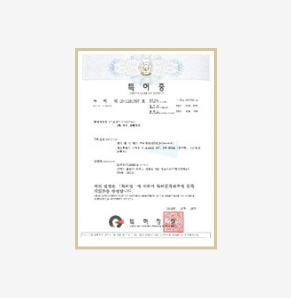
Tri-axial Displacement measuring device
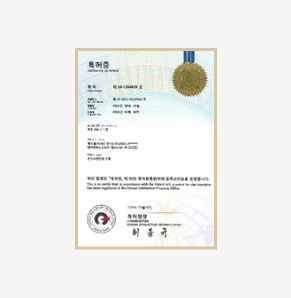
Load measuring system
Track Records
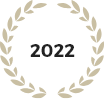
- Gangneung Eco Power
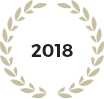
- GGP - Goseong Hai pp. #1,2
- KOSPO - Samcheok pp. #2
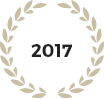
- KOEN - Yeongdong pp. #1
- KHNP – Shin-Hanul pp. #1
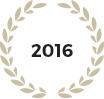
- KOMIPO - Boryeong pp. #7,8
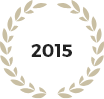
- KOEN - Yeosu pp. #1
- Malaysia | TNB Research - Janamanjung pp. #2
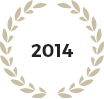
- KOSPO - Hadong pp. #1
- Hyundai Engineering / Doosan Enerbility - Yeongheung pp. #5,6
- POSCO E&C - Ansan pp.
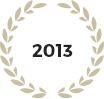
- KOEN - Samcheonpo pp. #3
- KOWEPO - Taean pp. #3
- KOMIPO - Boryeong pp. #4
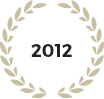
- KOEN - Yeogheung pp. $1~4
KOEN - Samcheonpo pp. #1,5
KOEN - Yeosu pp. #2 - KOMIPO - Boryeong pp. #4
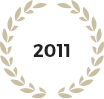
- KOEN - Yeongdong pp. #2
KOEN - Samcheonpo pp. #1~4
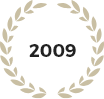
- Malaysia | TNB Research - Janamanjung pp. #3